Discover What is Porosity in Welding and Its Effect on Architectural Honesty
Wiki Article
The Science Behind Porosity: A Comprehensive Overview for Welders and Fabricators
Recognizing the complex mechanisms behind porosity in welding is vital for welders and makers aiming for remarkable craftsmanship. From the make-up of the base materials to the intricacies of the welding procedure itself, a wide variety of variables conspire to either exacerbate or relieve the existence of porosity.Understanding Porosity in Welding
FIRST SENTENCE:
Exam of porosity in welding reveals crucial insights right into the integrity and high quality of the weld joint. Porosity, identified by the existence of dental caries or voids within the weld steel, is an usual issue in welding procedures. These gaps, if not properly addressed, can jeopardize the architectural integrity and mechanical buildings of the weld, resulting in prospective failures in the completed item.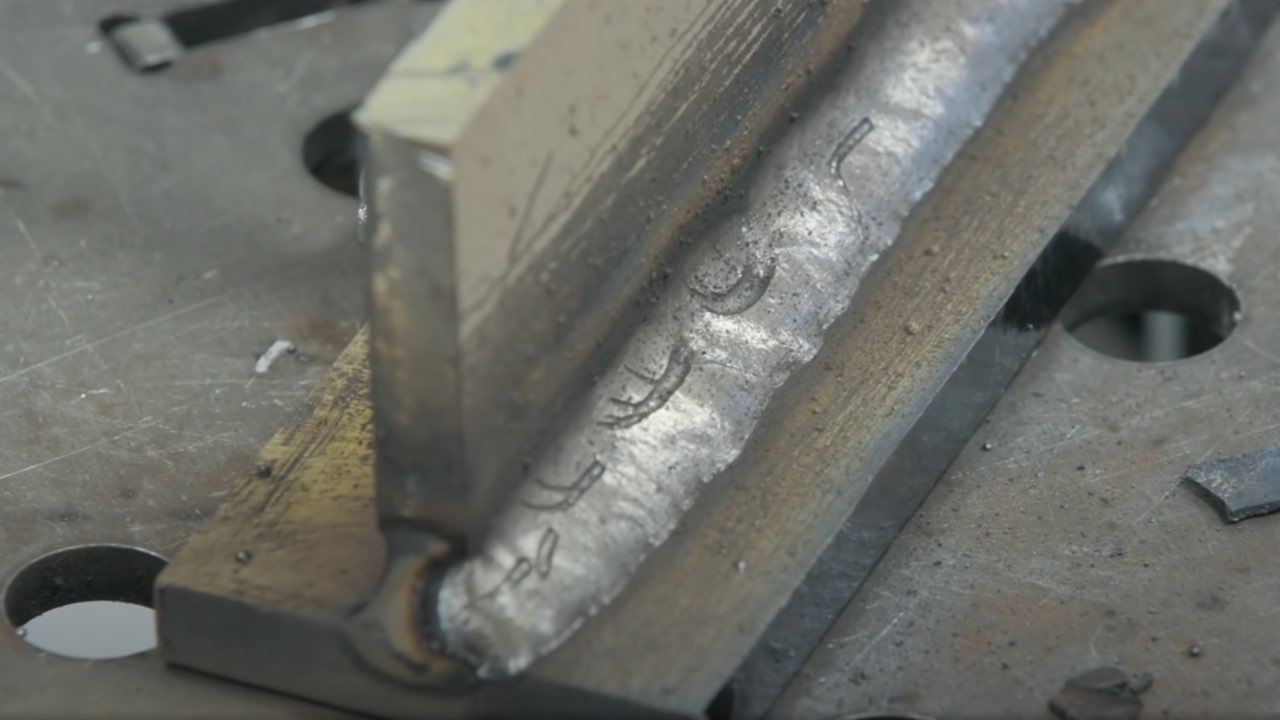
To identify and quantify porosity, non-destructive testing methods such as ultrasonic testing or X-ray assessment are often employed. These methods permit for the recognition of inner issues without endangering the integrity of the weld. By evaluating the size, shape, and distribution of porosity within a weld, welders can make informed decisions to improve their welding processes and attain sounder weld joints.
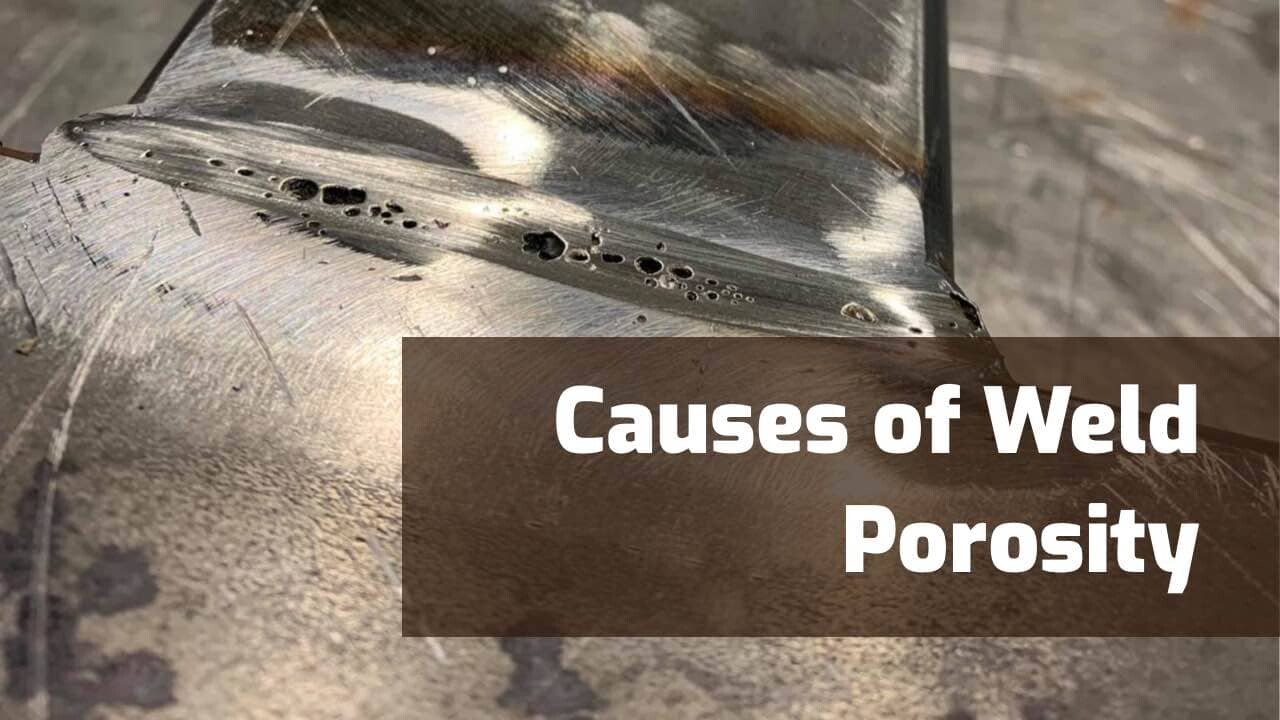
Variables Influencing Porosity Formation
The occurrence of porosity in welding is affected by a myriad of factors, ranging from gas securing effectiveness to the intricacies of welding specification setups. Welding parameters, consisting of voltage, current, travel rate, and electrode kind, also impact porosity development. The welding technique utilized, such as gas steel arc welding (GMAW) or shielded metal arc welding (SMAW), can influence porosity development due to variations in warmth distribution and gas protection - What is Porosity.Results of Porosity on Weld Quality
Porosity development considerably jeopardizes the architectural integrity and mechanical properties of welded joints. When porosity exists in a weld, it develops gaps or cavities within the material, lowering the overall strength of the joint. These spaces function as stress and anxiety focus points, making the weld a lot more at risk to cracking and failure my review here under load. The existence of porosity likewise compromises the weld's resistance to deterioration, as the trapped air or gases within deep spaces can react with the surrounding environment, resulting in deterioration gradually. Furthermore, porosity can prevent the weld's ability to withstand pressure or impact, further jeopardizing the overall quality and dependability of the bonded framework. In important applications such as aerospace, vehicle, or structural constructions, where safety and longevity are paramount, the detrimental impacts of porosity on weld high quality can have serious repercussions, emphasizing the importance of minimizing porosity through appropriate welding methods and procedures.Methods to Minimize Porosity
In addition, making use of the proper welding specifications, such as the appropriate voltage, present, and travel speed, is important in preventing porosity. Keeping a consistent arc length and angle throughout welding also helps lower the likelihood of porosity.
Using the appropriate welding strategy, such as back-stepping or utilizing a weaving motion, can additionally assist distribute warm evenly and lower the possibilities of porosity formation. By applying these methods, welders can effectively decrease porosity and produce top he has a good point notch bonded joints.
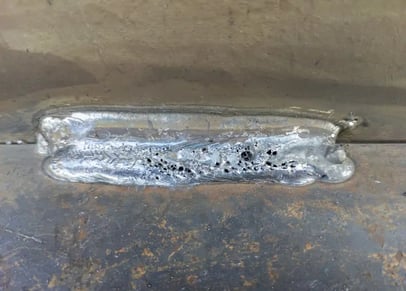
Advanced Solutions for Porosity Control
Carrying out advanced modern technologies and ingenious methods plays a pivotal duty in accomplishing premium control over porosity in welding procedures. One advanced option is making use of sophisticated gas mixtures. Securing gases like helium or a combination of argon and hydrogen can help in reducing porosity by offering far better arc stability and boosted gas protection. Additionally, utilizing advanced welding methods such as pulsed MIG welding or changed environment welding can additionally help alleviate porosity problems.An additional advanced remedy entails using advanced welding devices. As an example, using devices with built-in attributes like waveform control and advanced power resources can enhance weld top quality and decrease porosity risks. Moreover, the implementation of automated welding systems with exact control over parameters can substantially minimize porosity issues.
Furthermore, including sophisticated tracking see this website and inspection innovations such as real-time X-ray imaging or automated ultrasonic screening can assist in finding porosity early in the welding procedure, permitting immediate restorative actions. Overall, incorporating these innovative options can substantially enhance porosity control and enhance the overall quality of welded parts.
Final Thought
Finally, understanding the scientific research behind porosity in welding is crucial for welders and makers to create premium welds. By identifying the factors affecting porosity formation and implementing strategies to reduce it, welders can improve the general weld high quality. Advanced solutions for porosity control can better improve the welding process and make sure a strong and trusted weld. It is essential for welders to constantly inform themselves on porosity and implement best methods to achieve optimum results.Report this wiki page